Les principaux éléments en composites sont réalisés à partir de moules que se transmettent les constructeurs de Gazaile
Moules disponibles
(Moules récupérés début Juin 2025):
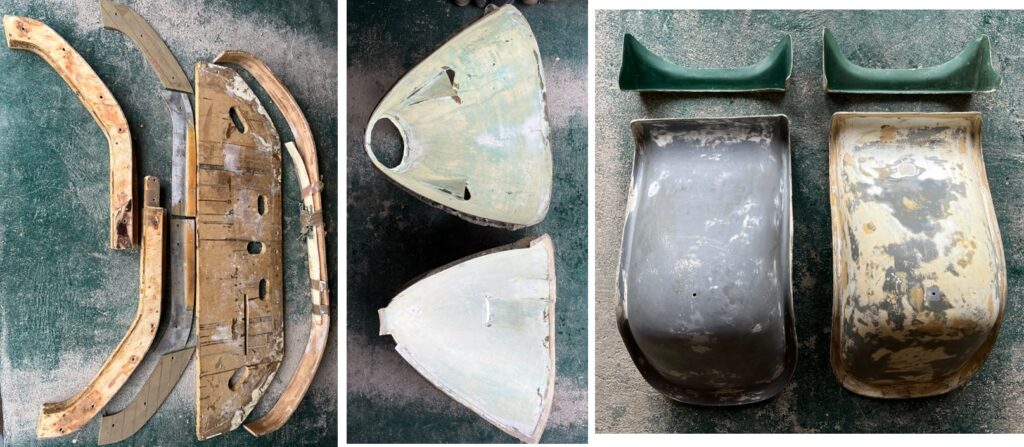
Gauche: train principal (inutilisé car j’avais déjà réalisé mon propre moule), Centre: capots moteur, droite: sièges (utilisés)
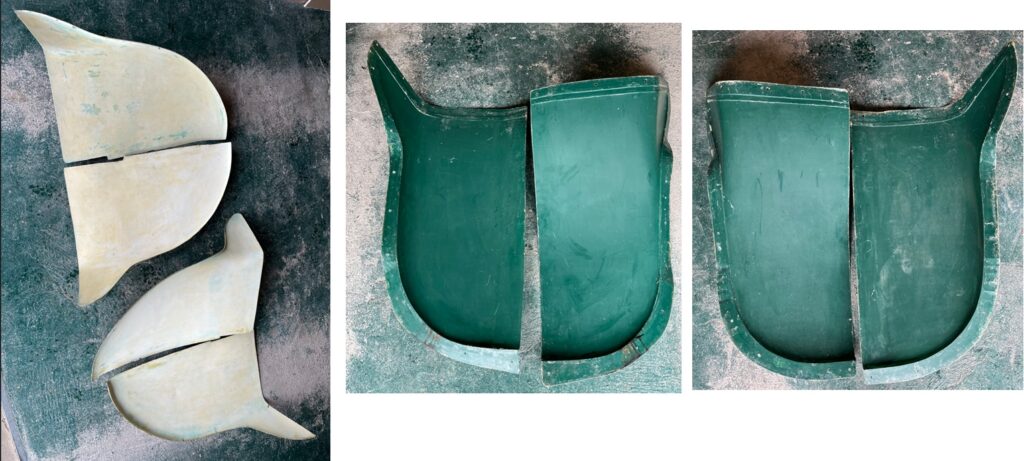
Winglets Avion et WingletsULM aile 1 M (Inutilisés dans mon cas car j’ai choisi de faire des saumons courts)
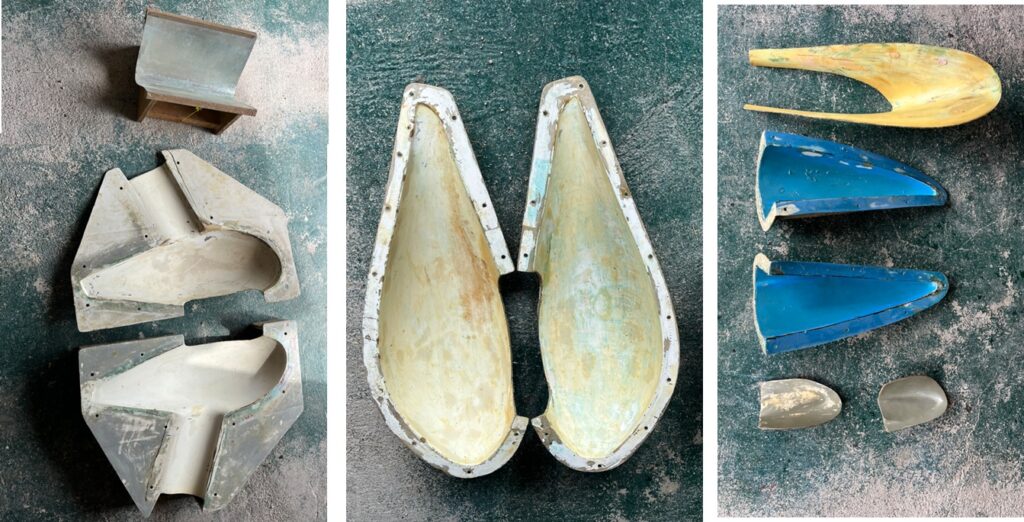
Gauche: Carénage roue avant pour avion (Inutilisé dans mon cas car un peu petit pour mon diamètre de roue) et V pour carénage jambe de train (utilisé), Centre: Carénage roue train principal (j’ai fais les carénages de la roue avant et des 2 roues du train principal dans ce moule), Droite: saumon empennage vertical et formes de queue du fuselage (utilisés).
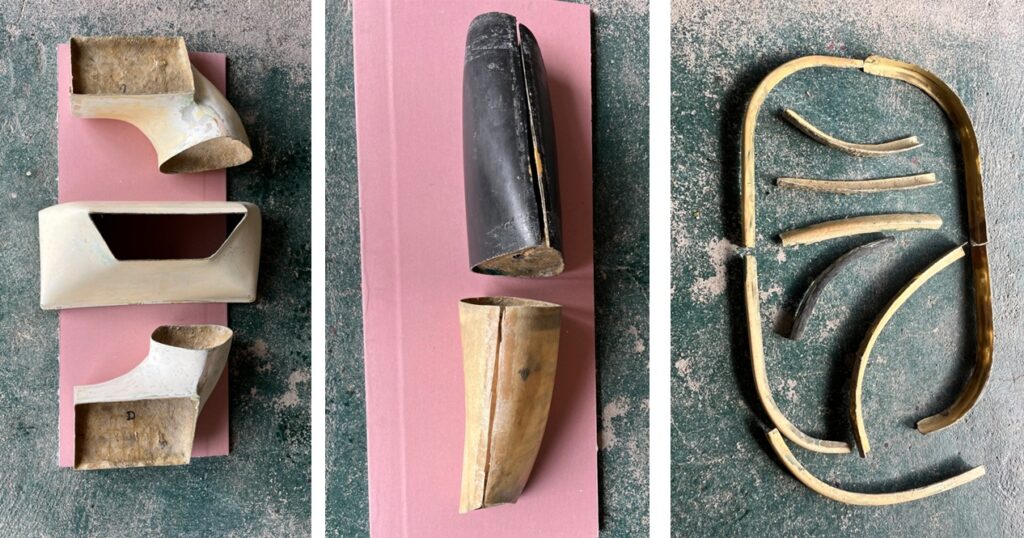
Gauche et centre: Gaines air refroidissement, Droite: Cornières capot/cloison pare feu (utilisés)
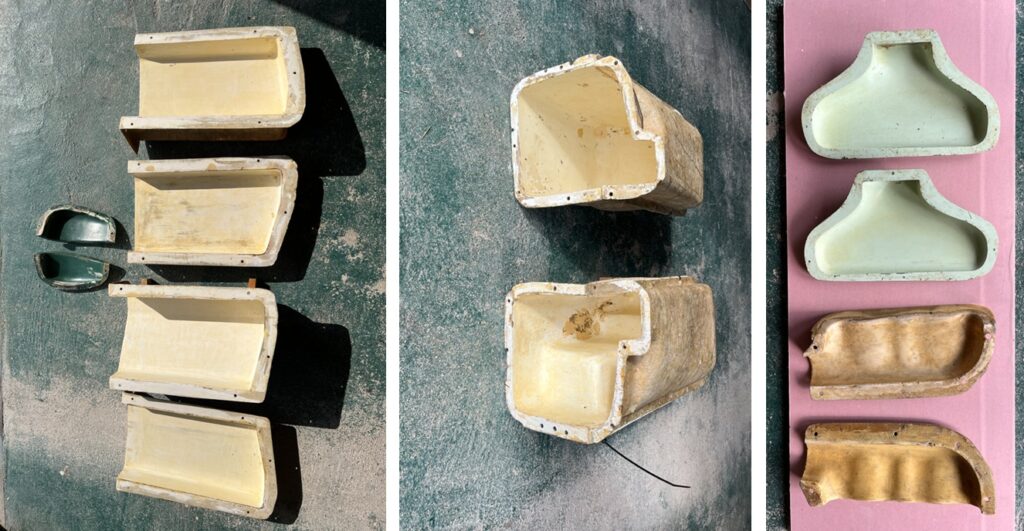
Gauche: Réservoir bas, Centre: Réservoir haut, Droite: Admission pour diesel . (Je n’ai pas utilisé ces moules, je ferai les réservoirs en fin de projet )
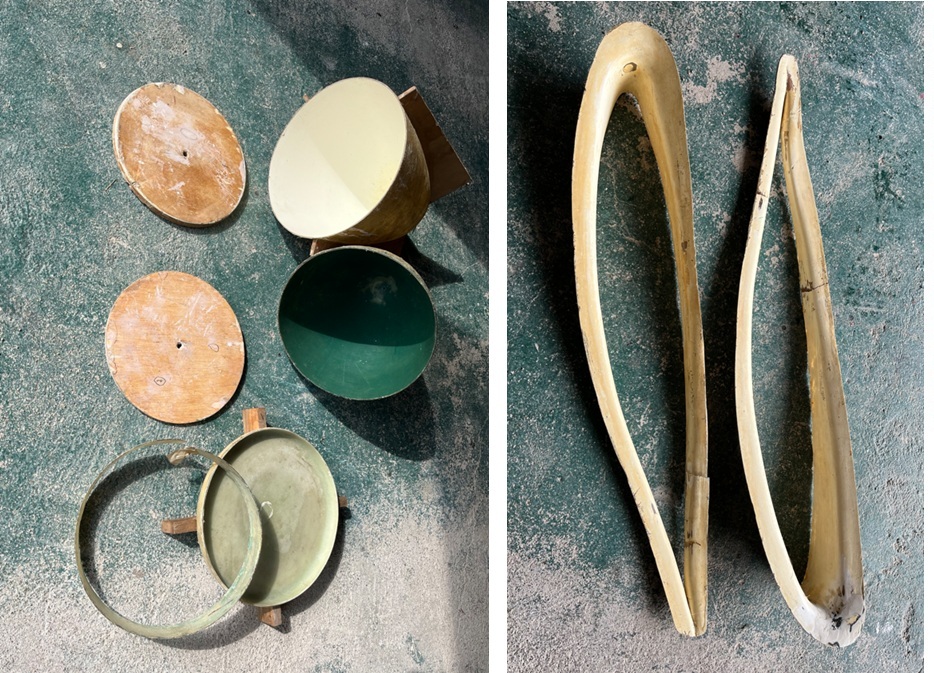
Gauche: Cône d’hélice (Inutilisé cans mon cas, j’achèterai le cône avec l’hélice), Droite: Karman d’aile avion
Pièces réalisées
Capots : 2 couches de sergé carbone 200 g + 1 taffetas 80 g. Bandes de renfort en polystyrène 5*20 mm recouvertes d’une sergé verre de 160 g. Poids de l’ensemble 1277 + 948 gr
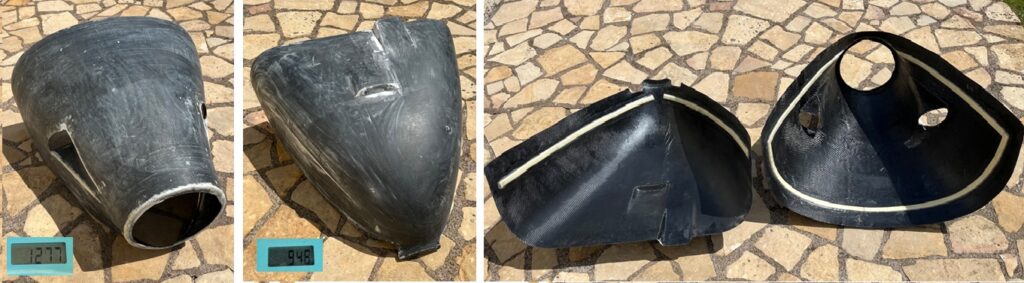
Sièges : 2 couches de sergé carbone 200 g + 1 taffetas 80 g. Renfort des contours en sergé carbone 200 g. Poids de l’ensemble 748+742+116+98 gr
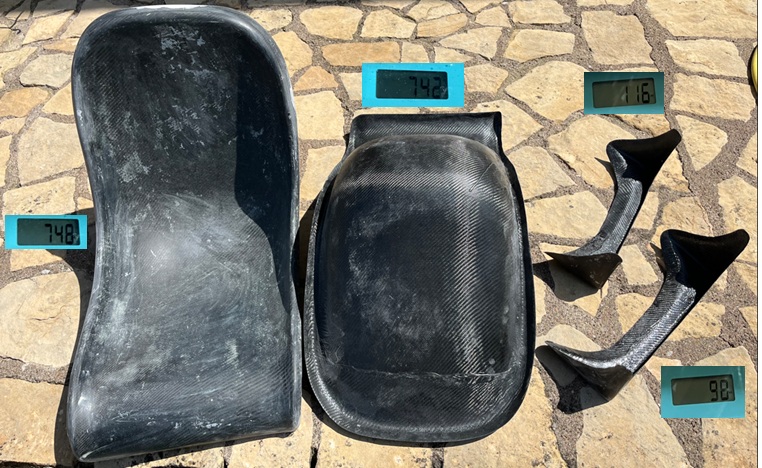
Gaines d’air : 1 couche de sergé carbone 200 g + 1 taffetas 80 g. Poids de l’ensemble 190+144+161+96+97 gr
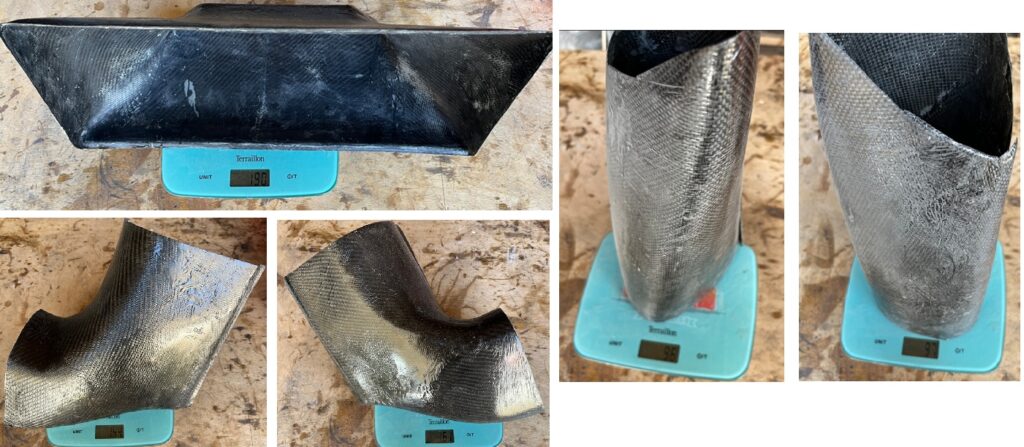
Carénages :
Le carénage de roue avant a été réalisé dans le moule des carénages du train principal (roue avant trop grosse pour le moule avion) . Donc 6 demi carénages fabriqués avec 1 couche de sergé carbone 200 g + 1 taffetas 80 g. Poids de l’ensemble 595 gr pour les 6 en sortie du moule. Une forme en vé 74 gr pour le carénage de la jambe de train avant.
Les 1/2 carénages sont ensuite assemblés dans les moules et renforcés avec des bandes de sergé carbone sur la périphérie et dans les zones de fixation. (288 et 296 gr carénages train principaux 260 gr carénage train avant).
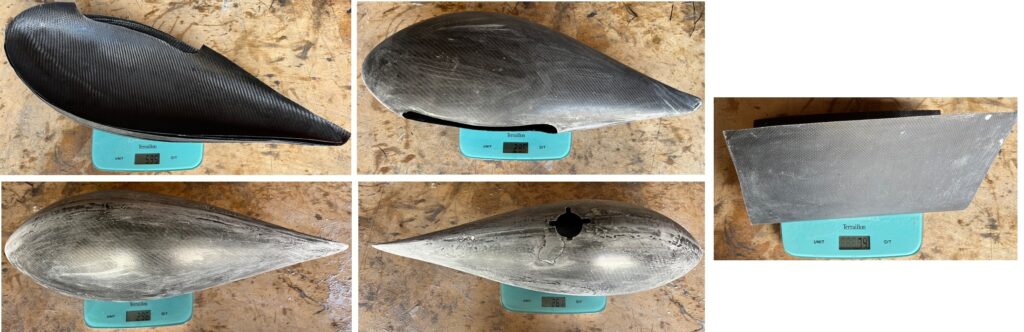
Eléments divers :
- Raccords de queue : 2 couches taffetas 80g Poids 16 + 17 gr
- Karman empennage V : 1 couche sergé verre 160 gr + 1 taffetas 80 gr. Poids 102 gr
- Profil de queue : 2 couches de sergé carbone 200 g + 1 taffetas 80 gr. Poids assemblé 214 gr
- Cornières pare-feu/capot : 3 couches sergé carbone 200 g : Poids 87 gr
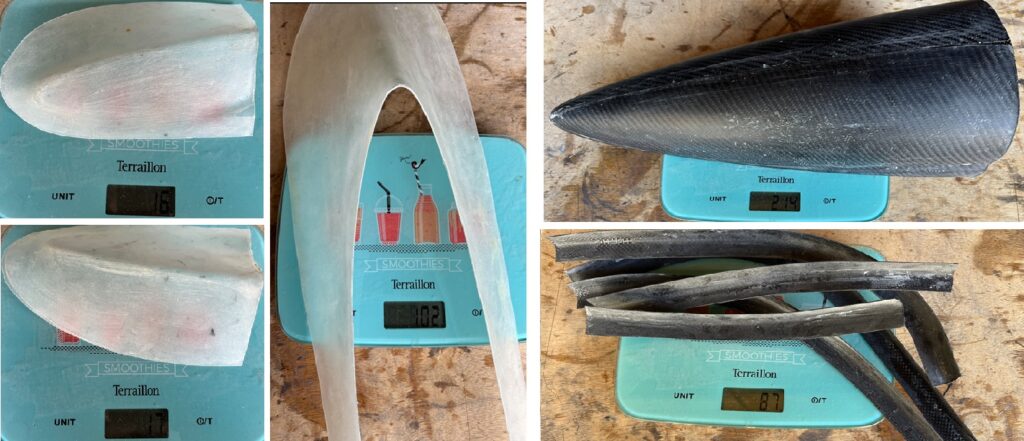
Retour d’expérience
Je n’avais aucune expérience en composite, les pièces ci-dessus ont été réalisées en 2 semaines. Ci dessous quelques points qui m’ont posés des soucis :
- Gants : Les gants nitrile bleu bas de gamme acheté chez Sicomin se déchirent très facilement (surtout si on manipule des pièces en carbone polymérisées). J’ai finalement utilisé des gants de mécanicien (nitrile structurés) beaucoup plus solides (7,5 Euros les 50 chez bricodepot)
- Echardes : Prévoir une pince à épiler pour ôter les innombrables morceaux de fibres qui se plantent dans les doigts
- Masque : J’ai commencé avec des masques type covid mais c’est inadapté. Utiliser un vrai masque à cartouches (surtout lors du ponçage du carbone) et prévoir un aspirateur
- Ciseaux : Le carbone et le verre se découpent bien avec un cutter et une règle ou avec des ciseaux normaux sur table, mais lorsque l’on doit couper les excédants de matière au bord des moules il faut des ciseaux micro dentés (on en trouve a 15 euros chez amazon) . Note : si on ne coupe pas au ras du moule, les couches de tissus font des vagues. La découpe avec des ciseaux normaux provoque un glissement du tissu et génère des plis et/ou des arrachements de fils. Pas de problèmes avec la micro denture la découpe est nette et sans glissement.
- Découpe : La découpe des excédants de matière après polymérisation est très facile avec une dremel et des disques de 33 mm (18 Euros les 10 chez Bricoman) . Le disque étant très fin, cela génère peu de poussière. Par contre, il faut au préalable bien couper aux ciseaux les fibres non enduites de résine qui dépassent (cf image ci dessous) car c’est dangereux quand une fibre s’enroule autour du mandrin.
- Ponçage : Les bords des pièces étant très agressifs, les feuilles de papier de ponçage se déchirent facilement. J’ai utilisé des bandes pour ponceuse à bande pour le ponçage des champs.
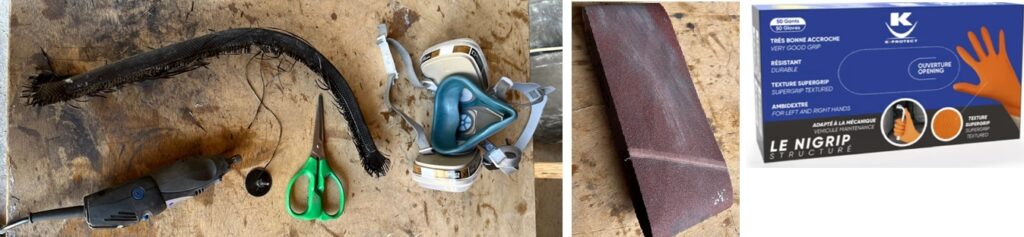
Renfort capots : J’ai galéré pour mettre en place les renforts capots.
1 ier essai: collage d’une bande de polystyrène au double face puis marouflage aves un sergé verre 160g => Décollement du double face (sans doute que la colle a été dissoute par la résine) et formation de bulles d’air .
2 ieme essai: collage d’une bande de polystyrène à la résine, attente séchage, puis marouflage aves un sergé verre 160g => formation de bulles d’air. Il faisait chaud, je pense qu’avec la réaction de polymérisation exothermique l’air présent dans le polystyrène se dilate et provoque le décollement du tissu.
3 ieme essai: collage d’une bande de polystyrène à la résine, attente séchage, puis recouvrement avec de la résine sans tissu (une bonne couche pour bien rendre étanche) et attente séchage puis enfin marouflage aves un sergé verre 160g=> Résultat OK