La transmission à l’hélice est assurée par un réducteur à courroie fixé et accouplé au bloc moteur par des colonnettes et un accouplement élastique (flector) .
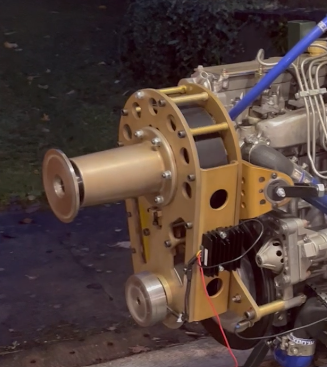
Fabrication des pièces
La plupart des pièces du réducteur (Arbres, platines, roulements et porte roulement, nez de réducteur, poulies, courroie) sont disponibles auprès du CSA (association des constructeurs de Gazaile). J’ai donc acheté le maximum de pièces.
J’ai usiné les pattes de fixation, certaines colonnettes, entretoises et rondelles complémentaires et effectué les perçages et filetages sur les pièces du CSA.
Note : Attention, les trous recevant les vis de fixation du nez dans la platine avant sont en M8 (les vis servent de goujons) ne pas percer à 8 mm. J’ai fait la bêtise et j’ai du fabriquer des insert M8 pour corriger.
Ci dessous les pièces constituants le corps du réducteur et les entretoises de fixation au moteur.
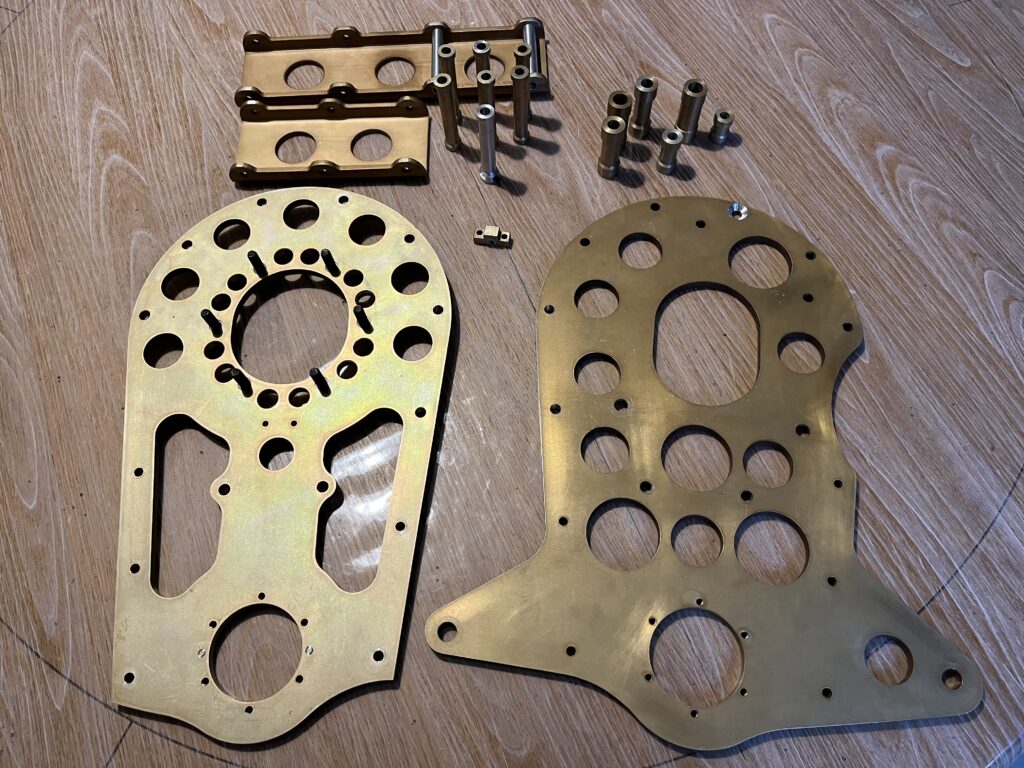
Ci dessous les composants de l’arbre d’hélice (Nez réducteur, arbre, roulements, entretoise entre roulements poulie et clavette)
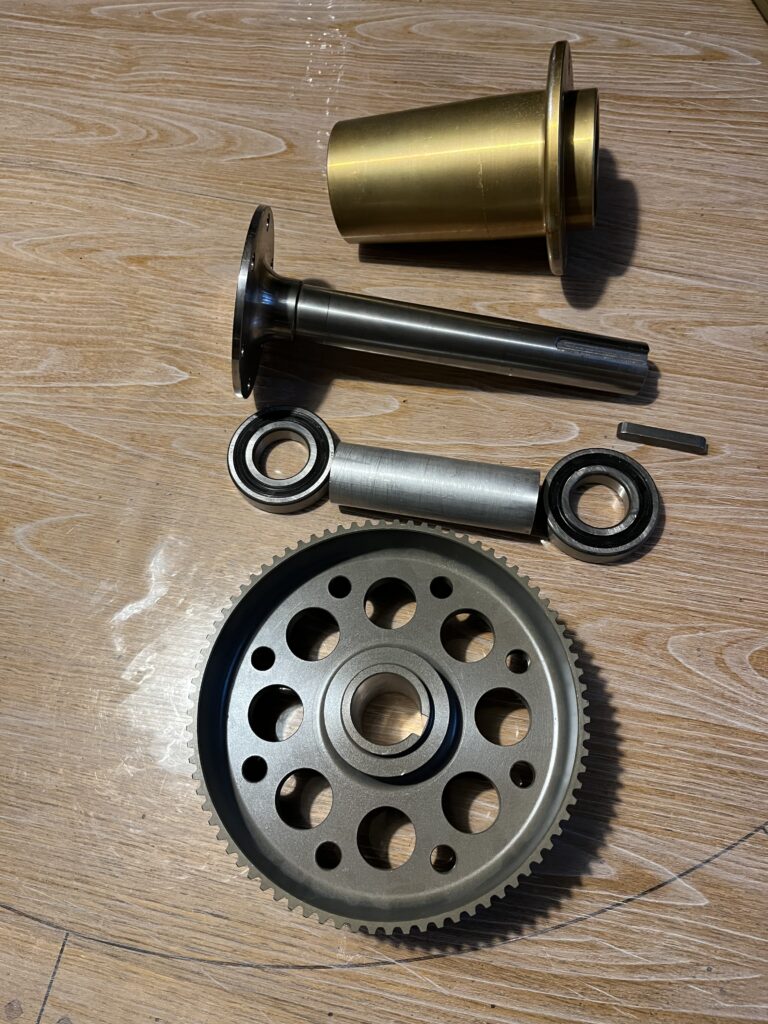
Ci dessous les composants de l’arbre moteur.
Partie droite on voit l’arbre bas avec un roulement déjà monté. Le porte roulement arrière, la poulie et sa clavette, puis une entretoise, le roulement avant et son porte roulement et enfin la butée de serrage du roulement et la cloche de l’alternateur. La portée cylindrique de l’arbre qui reçoit le flector est moletée pour améliorer la transmission des efforts.
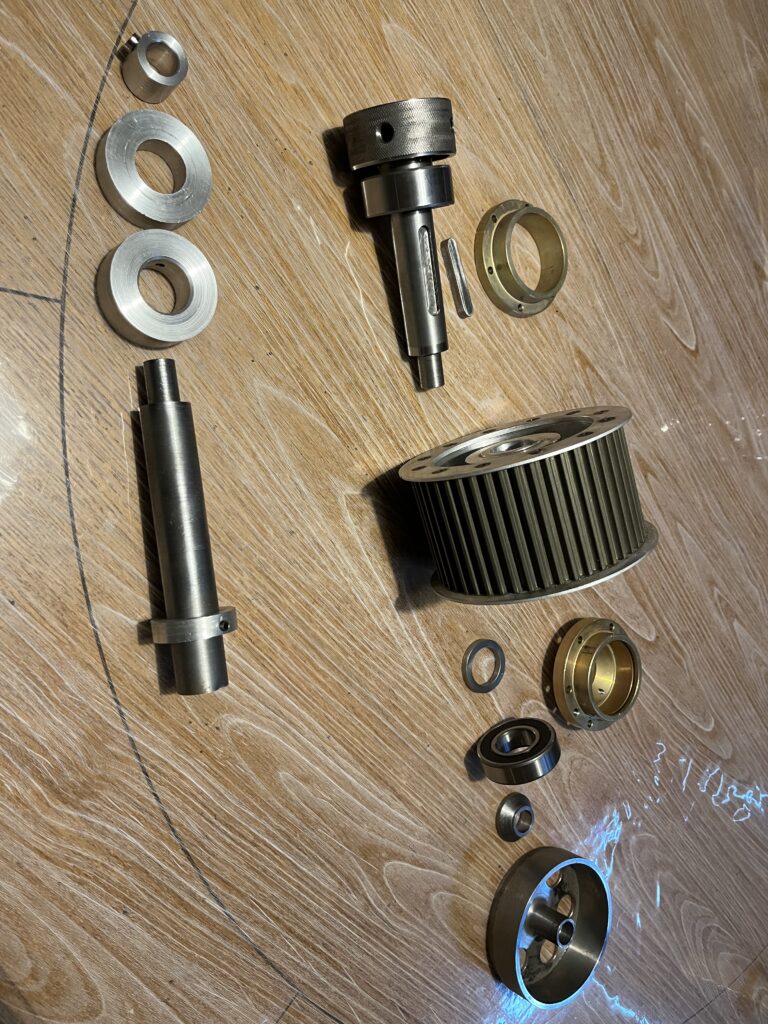
Coté gauche, ce sont des pièces qui ont été fabriquées pour aider l’assemblage soit :
- Un faux axe et 2 faux roulements usinés à des diamètres voisins des valeurs réelles et permettant de monter l’ensemble dans le corps du réducteur sans efforts pour vérifier les cotes avant les opérations de montage/frettage.
- Une bague guide clavette pour aider la mise en place de la poulie à chaud.
Pré-montage
Le perçage des trous de fixation des platines du réducteur sur le bloc moteur doit être précis pour assurer un bon alignement avec le volant d’inertie et limiter les contraintes sur l’accouplement élastique. J’ai procédé comme suit:
- Usinage de vis avec une tête en pointe et usinage d’une pige de centrage
- Mise en place des vis sur le bloc et de la pige sur l’axe du volant moteur
- Présentation de la platine réducteur sur la pige et marquage de la position des vis (pointage en frappant sur la platine)
- Perçage des trous de fixation dans les platines (Les 2 platines sont accolées et centrées l’une par rapport à l’autre en emboitant le support de roulement arrière dans les 2 platines
Après perçage des différents éléments, la structure du réducteur est montée sur le bloc pour vérifier le positionnement et définir la géométrie des pattes de fixation des tirants moteur.
Des modèles sont réalisés dans de la tôle d’aluminium fine et malléable pour obtenir des empreintes qui aideront à la découpe et au pliage
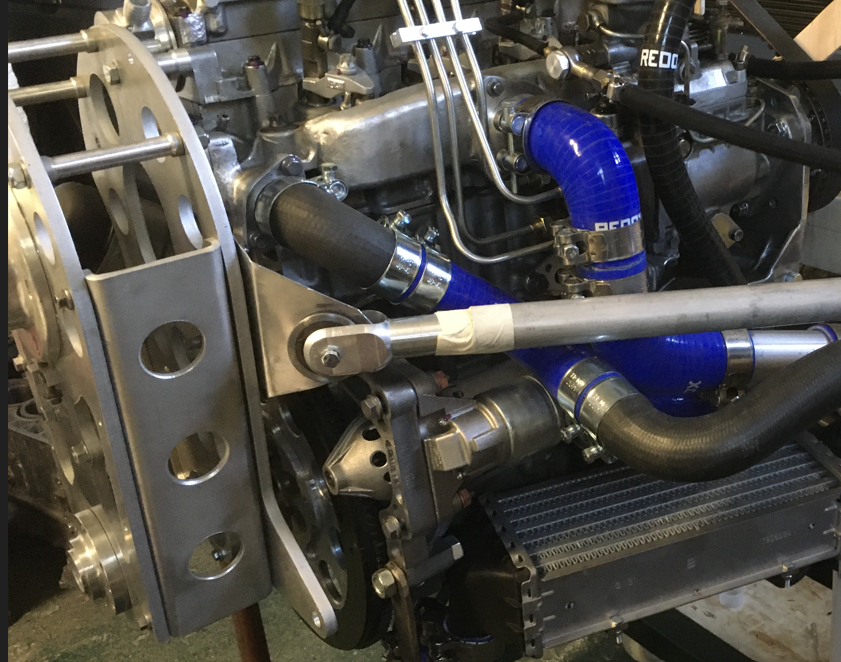
Après traçage et découpe grossière sur de la tôle alu de 5mm, les plaques sont pliées à la presse (avec un rond pour conserver un rayon de courbure de 10 mm) après avoir effectué une trempe fraîche.
Chaque pattes étant constituée de 2 tôles en sandwich, celles ci sont assemblées après pliage et avant la finition des contours et perçages.
Ci-dessous les pattes terminées avec les silentblocs montés.
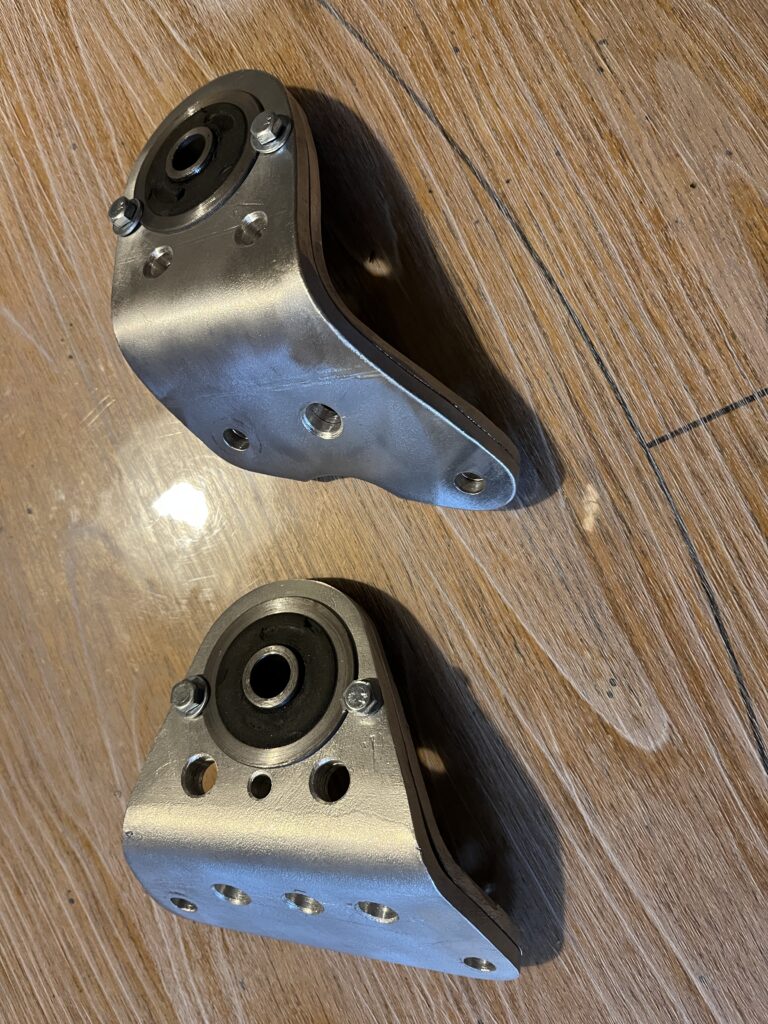
La patte de fixation coté gauche est fixé avec les vis du U qui à l’origine sont prévus en M6. J’ai repercé à 8 mm et ajouté 2 entretoises de renfort pour utiliser des vis M8 et prévenir des déformations dues aux efforts exercés par les tirants.
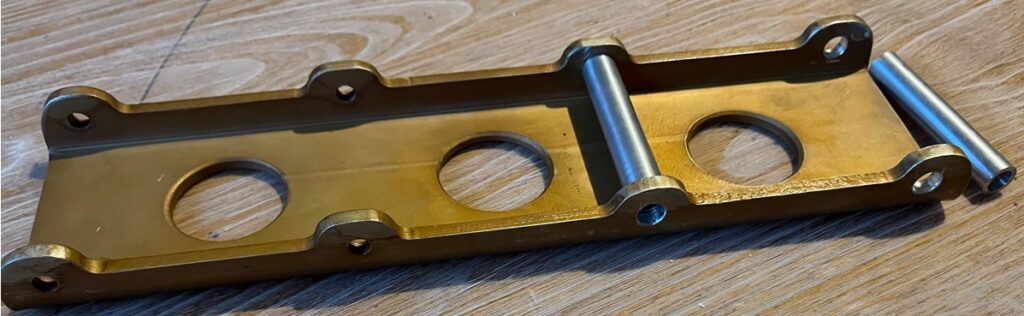
Le moteur étant équipé d’un piège à huile, la vis de la colonnette supérieure doit être noyée dans là platine arrière du réducteur à l’aide d’une vis à tête fraisée. La vis étant inaccessible après montage, j’ai réalisé une colonnette spécifique avec une vis de pression et des méplats pour pouvoir maintenir la vis pendant le serrage de l’écrou.
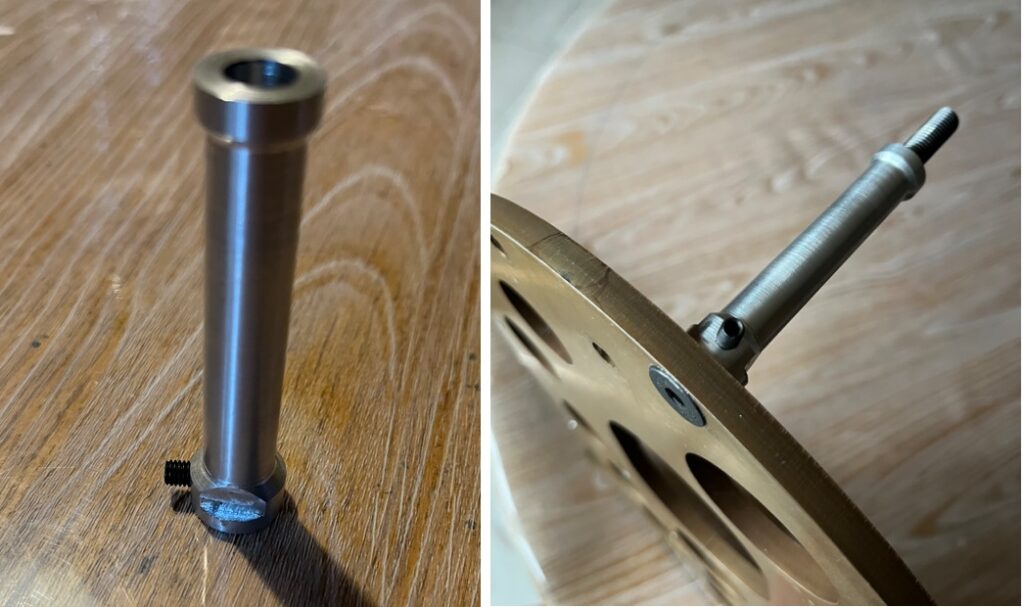
Les éléments aluminium sont ensuite traités à l’alodine.
Arbre /poulie moteur
Vérifications avant montage
- Assemblage du réducteur avec l’arbre bas complet en utilisant les faux roulements et le faux axe pour vérification du jeu entre la poulie basse et les platines (le faux roulement arrière est bloqué sur le porte roulement par une vis de pression intérieure) . Vérification du jeu de serrage de la butée devant le roulement avant.
- Le flector étant en place sur le volant moteur : Assemblage du réducteur sur le bloc en utilisant l’arbre bas réel (sans poulie) et les faux roulements . Vérification du bon positionnement des trous du flector en face des filetages de l’arbre moleté.
Montage des composants
- Emmanchage du roulement arrière sur l’arbre (à l’aide d’une tige filetée et un manchon de guidage)
- Mise en place du porte roulement arrière
- Montage de la clavette et montage de la bague de guidage. (Hauteur de clavette préalablement réduite pour conserver un jeu 0,5mm afin de faciliter l’insertion de la poulie à chaud)
- Préparation pour frettage de la poulie à chaud (établi près du four, gants et marteau + cales en cas de problème. Repérage du sens de la poulie pour ne pas faire d’erreur.
- Frettage de la poulie : Chauffage de la poulie à 250° 1H30, puis insertion sur l’axe. C’est un peu stressant mais en fait ça rentre tout seul.
- Montage du roulement avant dans son porte roulement. (Mettre la butée avant dans le porte roulement puis le roulement puis le circlips)
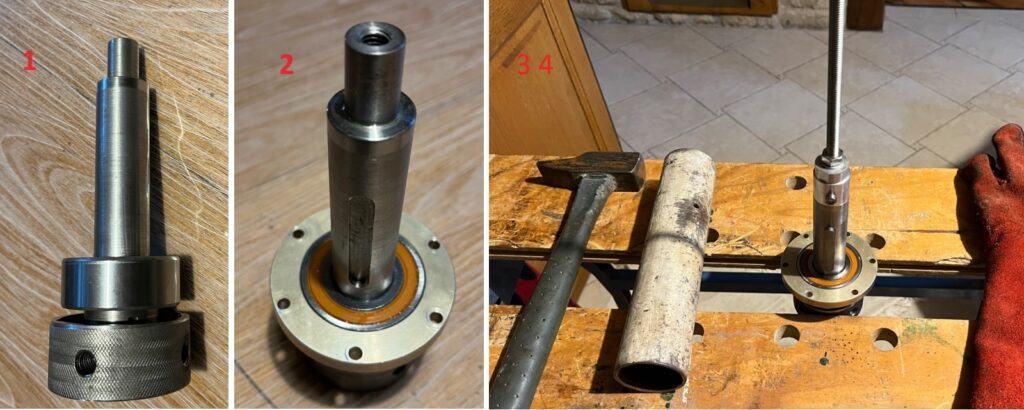
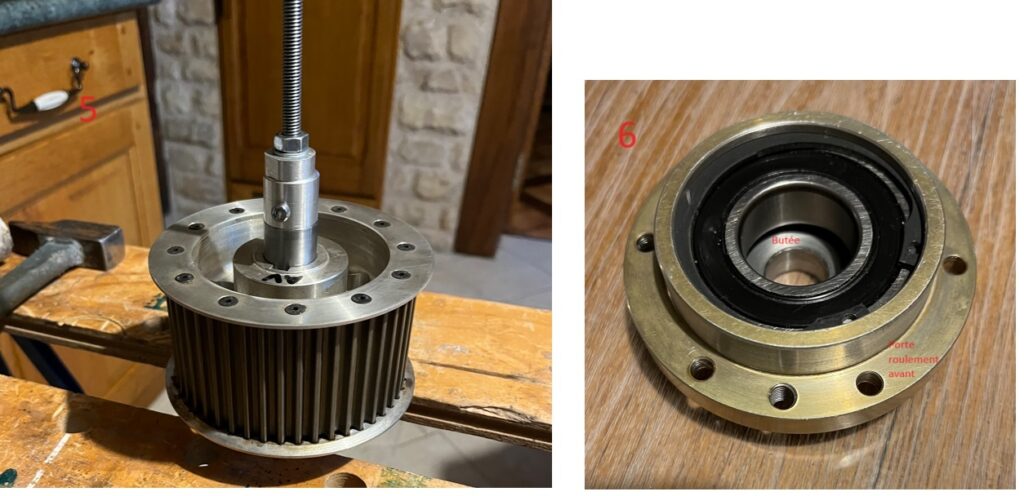
L’arbre bas est alors prêt pour l’assemblage final sur le corps du réducteur.
Arbre hélice
Montage de l’arbre d’hélice sur le nez
- Emmanchage du roulement avant (à l’aide d’une tige filetée et un manchon de guidage)
- Mise en place de l’entretoise de 125 mm qui sépare les roulements sur l’arbre
- Mise en place du nez de réducteur sur le roulement avant (chauffage préalable du nez à 100° pour faciliter son insertion )
- Emmanchage du roulement arrière (à l’aide d’une tige filetée et un manchon de guidage) : j’ai du finir l’emmanchage à la presse car les derniers mm étaient très difficiles (le filetage de la tige filetée de 12 mm avait cassé). ATTENTION LORS DE L’UTILISATION DE LA PRESSE A CETTE ETAPE , NE PAS FORCER QUAND LE ROULEMENT ARRIVE EN BUTEE DANS SON LOGEMENT.
- Mise en place du circlips
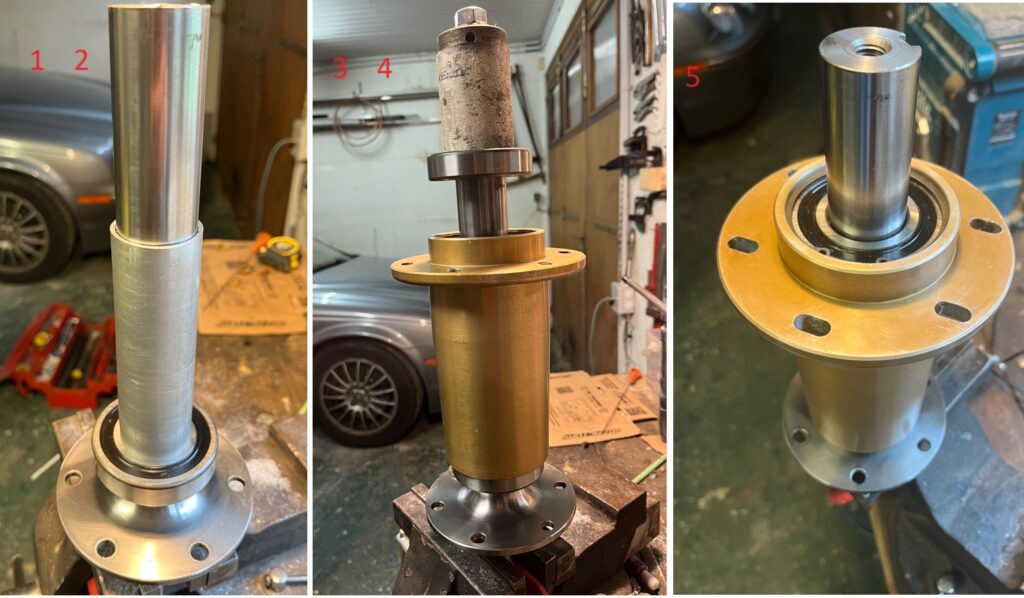
Montage du nez sur la platine avant
- Mise en place des vis de maintient du nez de réducteur et collage des vis à l’araldite (Ces vis servent en fait de goujons)
- Fixation du nez sur la platine avec des écrous freinés et rondelles
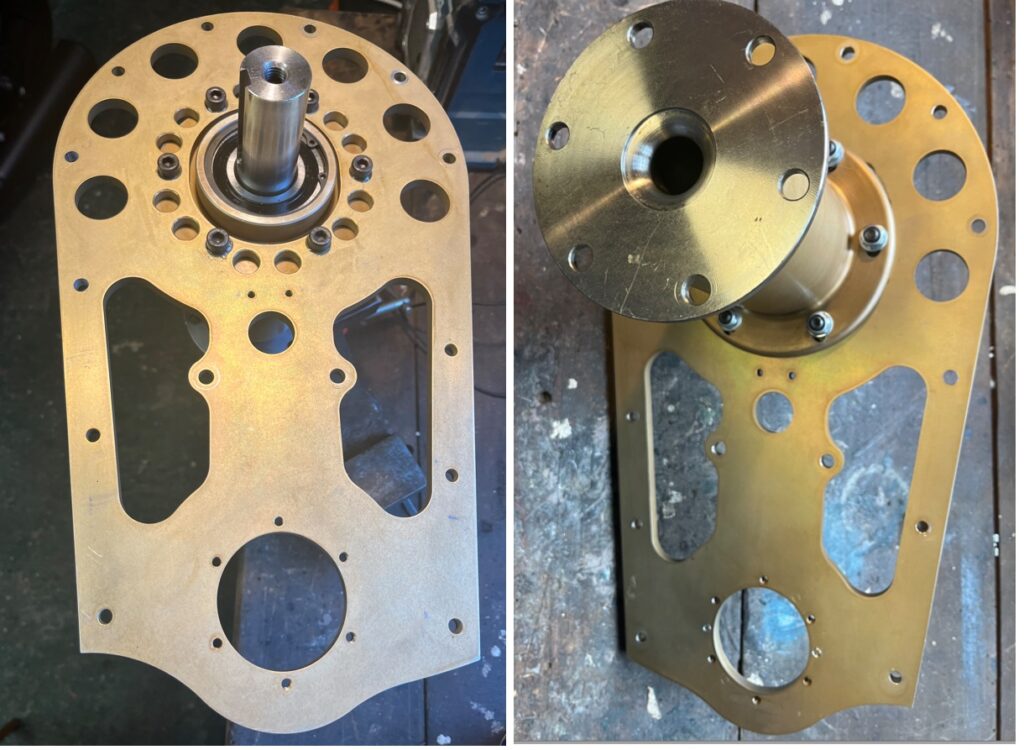
Frettage de la poulie arbre d’hélice
- Montage de la clavette (Hauteur de clavette préalablement réduite pour conserver un jeu 0,5mm afin de faciliter l’insertion de la poulie à chaud)
- Chauffage de la poulie à 250° 1H30, puis insertion sur l’axe.
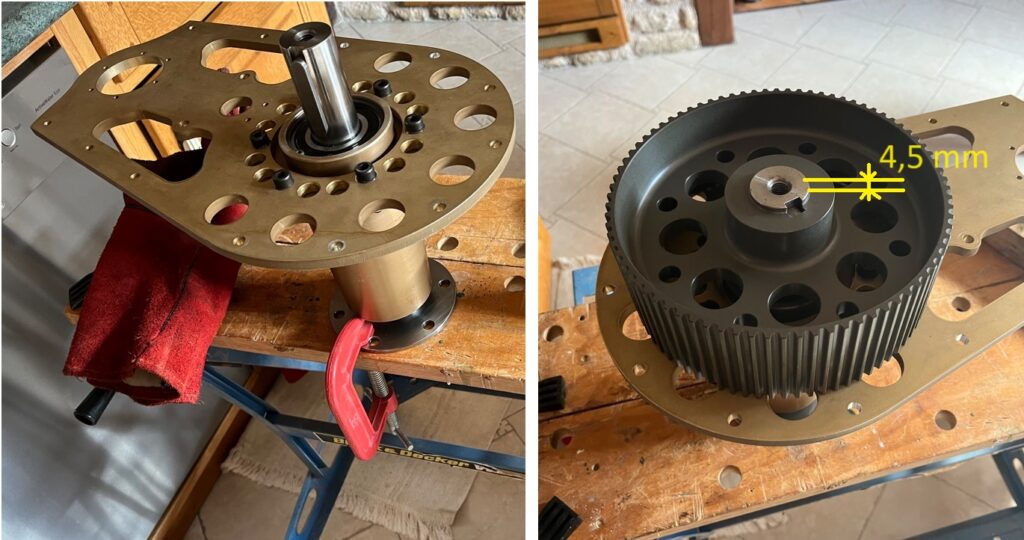
CATASTROPHE : L’arbre qui devrait être en retrait de la poulie d’envire 0,5 mm dépasse de 4,5 mm. Cela signifie que lors du travail à la presse, le roulement avant qui doit rester flottant est venu en butée dans la portée en bout de nez. J’ai écrasé l’entretoise inter roulements avec ma presse de 20 tonnes. (A l’origine cette entretoise est fabriquée dans un tube d’aluminium pas très épais). Il faut corriger le problème car, en l’état, les roulements subiront de fortes contrainte axiales sous l’effet de la dilatation des matériaux.
Démontage et correction du problème
- Retrait de la poulie: L’ensemble est chauffé au four à 250 °C. J’ai mis un système de ressort et tirants pour appliquer une force d’extraction de la poulie pendant la chauffe. Cela permet de voir quand c’est suffisamment chaud (la poulie s’extrait toute seule après 45 min au four)
- Extraction de l’arbre et des roulements à la presse. J’ai réalisé 2 plaques d’accueil en bois avec des 1/2 trous de 90mm pour ne pas blesser le nez pendant l’extraction.
- On constate bien que l’entretoise a perdu 5 mm (120 au lieu de 125 mm)
- Usinage d’une nouvelle entretoise plus épaisse (Réalisée en 2 parties de 62,5 mm pour faciliter l’usinage)
- Achat de nouveaux roulements (ils ont subit une forte contrainte à la presse et ont été surchauffés au four)
- Remontage en évitant d’écraser l’entretoise (cf séquence ci-dessous)
- Mise en place de la rondelle et vis de fixation en bout d’arbre.
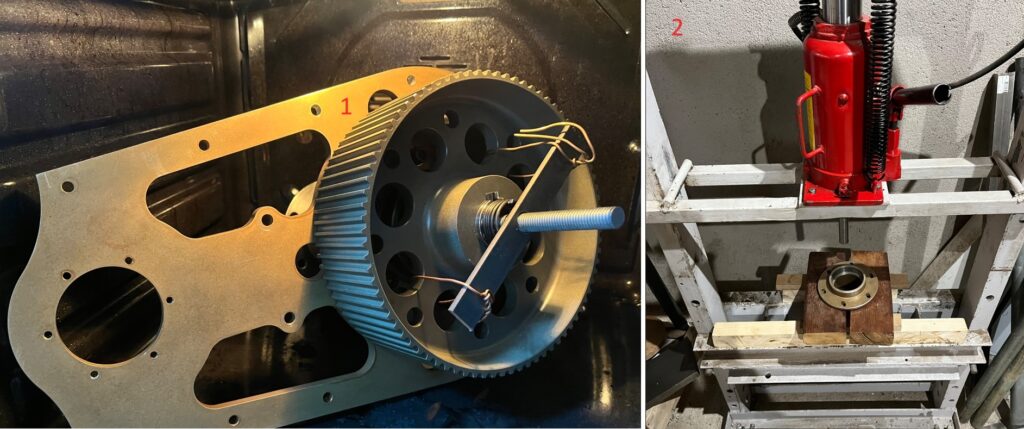
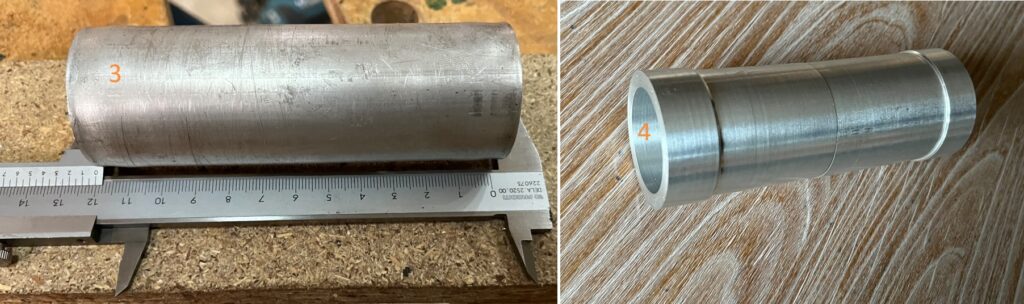
6 Séquence d’assemblage des roulements arbre hélice

Après remontage, l’arbre haut est prêt pour l’assemblage final
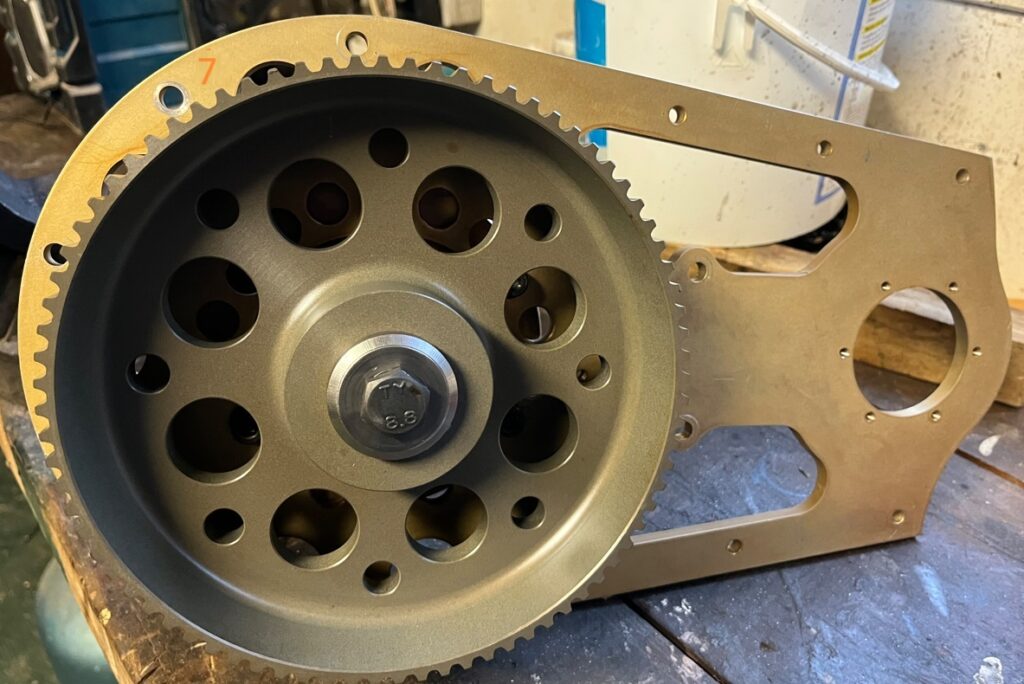
Point positif : Cette erreur m’a permis de constater que le désassemblage des axes n’est pas trop compliqué (si on a une presse) et est réalisable sans dommage, ce qui est rassurant pour les opérations de maintenance futures.
Assemblage et réglage
Assemblage
- Montage du flector sur le volant moteur et serrage au couple (70 mN et frein a filet bleu). La longueur des vis a été ajustée avant montage du volant d’inertie pour ne pas dépasser car il y a un risque de détérioration du joint spi sortie moteur.
- Montage de la platine arrière du réducteur sur le bloc avec vérification du centrage grâce à une pige emboitée sur l’arbre de sortie du moteur.
- Montage de l’arbre bas et fixation du porte roulement arrière sur la platine. Les vis de fixation sont accessibles au travers des trous d’allègement de la poulie du réducteur.
- Le nez de réducteur étant en position basse, mise en place de la courroie de transmission sur la poulie haute
- Insertion de la courroie sur la poulie basse et assemblage de la platine avant avec les colonnettes et U. Les vis sont ajustées en longueur pour limiter le cumul de petits surpoids. Les écrous sont de type freiné avec rondelle d’appui.
- Mise en place des pattes de tirants.
- Insertion de la cale entre poulie basse et roulement avant
- Montage du porte roulement avant de l’arbre bas.
- Serrage final des vis du réducteur
- Utilisation d’une entretoise et d’une rondelle temporaires et serrage de l’arbre bas en attendant l’assemblage de l’alternateur
- Vérification de la libre rotation du réducteur
- Vérification du positionnement des trous du flector par rapport aux trous du moyeu moleté de l’arbre réducteur.
- Mise en place des vis du flector sur l’arbre réducteur et serrage au couple (70 mN et frein a filet bleu). La longueur des vis a été ajustée avant pour s’assurer que la prise de filet soit maximale mais que le bout des vis ne touche pas le fond des trous filetés.
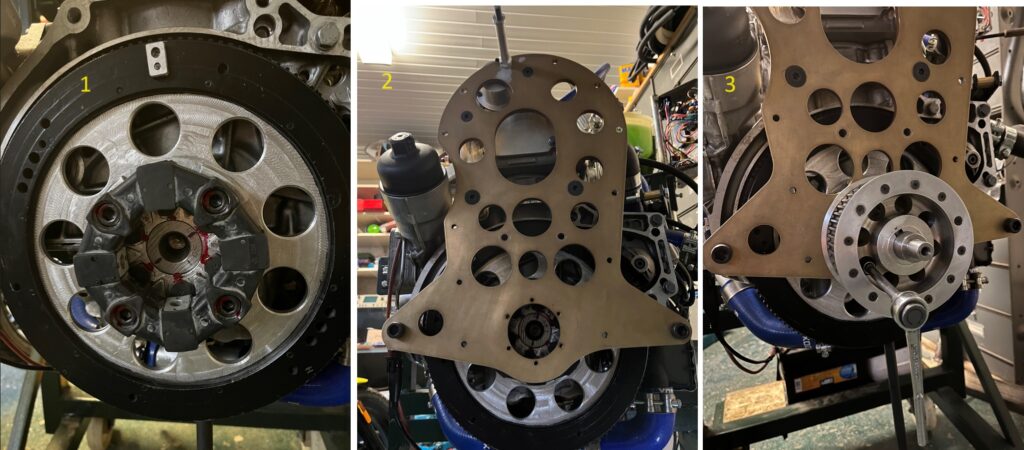
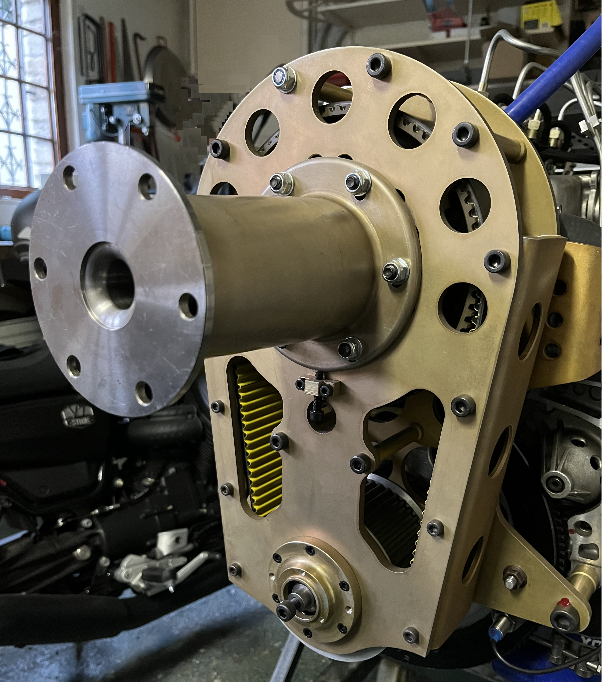
Réglage
J’ai réalisé un outil de contrôle de la tension courroie (manchon au diamètre des trous d’allègement U réducteur avec un axe de diamètre 25 mm coulissant gradué tous les 2,5 mm) qui se place dans le trou d’allègement du U de réducteur coté droit (à mi hauteur de la courroie). Le réglage est fait pour obtenir un débattement d’un cm en quand on appuie fermement sur l’outil (mais pas trop).
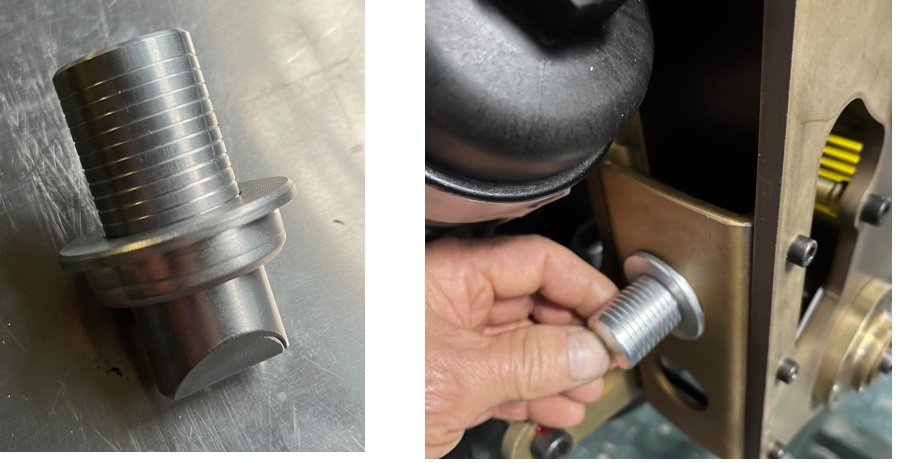
Alternateur
La cloche, le stator et les aimants constituant l’alternateur ainsi que le régulateur de tension proviennent du CSA (association des constructeurs de Gazaile).
Les 10 aimants (Diam 10mm épais 4mm) sont collés dans la cloche avec une colle bi composant en alternant pôles + et pôles – puis noyés dans de la résine chargé au floc. Le moule pour la résine est constitué d’une bande de tôle fine (boite de conserve) recouverte de scotch paraffiné qui vient se coller sur les aimants. La cloche est ensuite équilibrée avec un axe de 8 mm traversant la cloche et test sur 2 plats aluminium horizontaux : ne pas utiliser de réglet métallique car les aimants perturbent le test. L’équilibrage est fait par retrait de résine a l’aide d’une fraise.
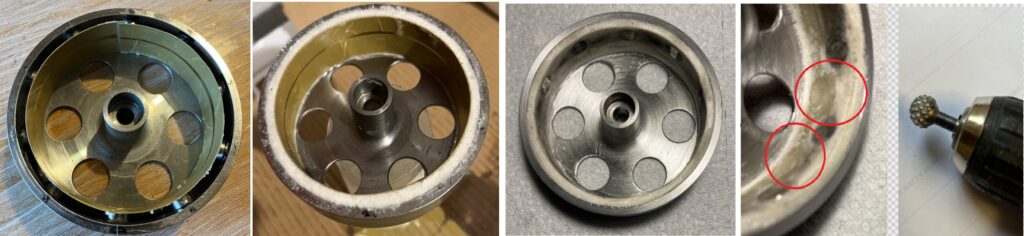
Des fils souples sont soudés en sortie du bobinage stator au plus près des bobines puis le stator est imprégné à la résine . Les points de jonction entre cuivre rigide et fils souples son noyé dans la résine.
Le régulateur est positionné sur le U gauche du réducteur, la connexion régulateur alternateur est réalisé par soudure + gaine thermo rétractable. Les fils sont solidarisés par de la gaine et des colliers.
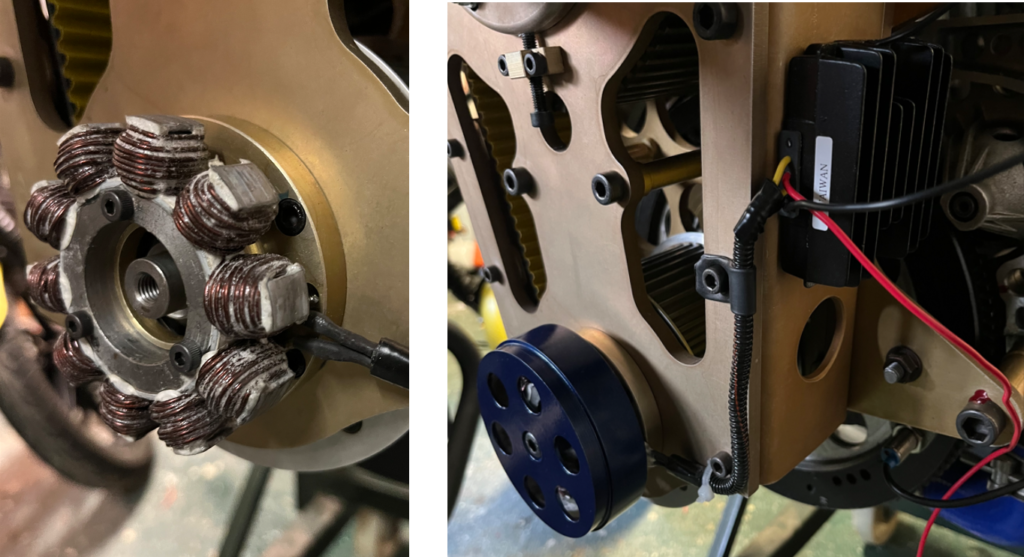
Capteur vitesse
Le capteur vitesse est intégré sur le flasque réducteur face au volant moteur. La distance flasque/volant est un peu trop élevée pour une fixation directe. J’ai fabriqué une pièce en aluminium permettant un montage rigide est bien intégré. Un des écrou du capteur est prisonnier dans la pièce ce qui facilite le serrage.
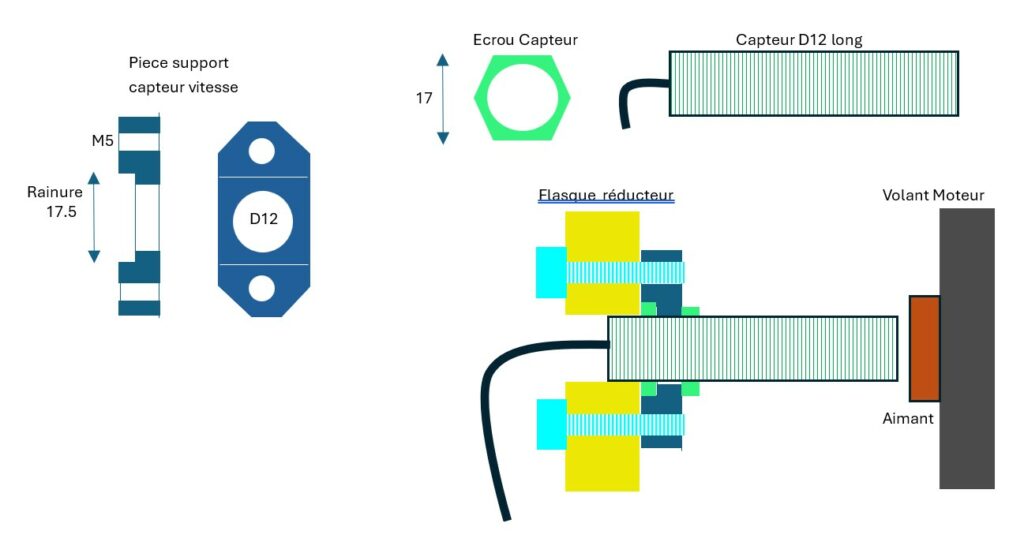
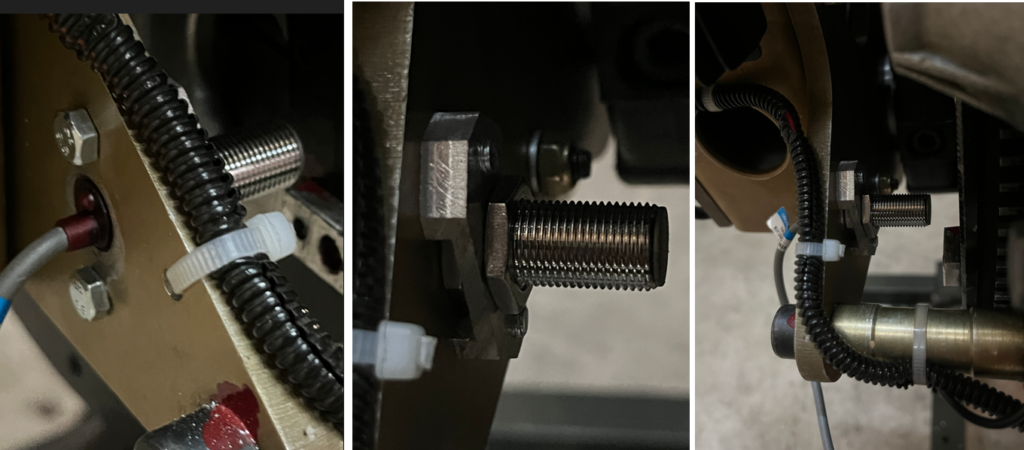
Essais
Dès les premiers tests de rotation moteur en marche, je constate que la courroie frotte légèrement sur les portées des U réducteur. J’ai du démonter , limer les angles des portées et remonter les U réducteur.
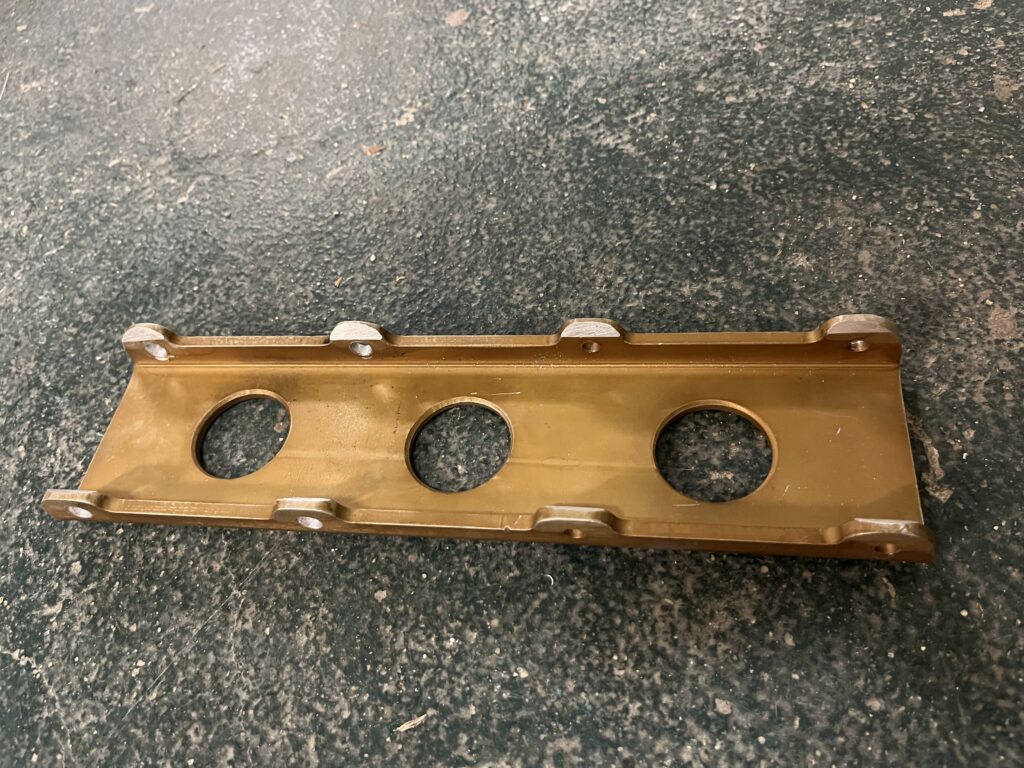
Après correction, plus de souci, la courroie est bien centrée
L’alternateur commence a débiter du courant vers 1700 rpm avec 0.7A, le courant passe à 2,5 A à 2160 rpm (sur une batterie faible à 11,8V).
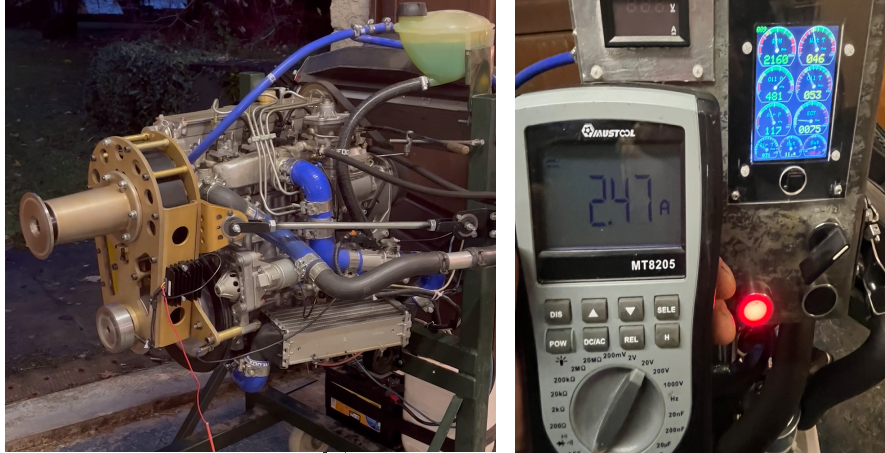